Importance of choosing the right 3-layer system
Performance characteristics of your turnout gear are determined by the choice of combined fabric components. Each layer serves specific functions and, as a composite, is expected to provide you with superior heat and flame protection, while maximizing mobility and flexibility.
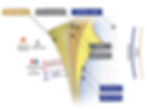
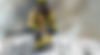
DEBUNKING YOUR TURNOUT GEAR
Dozens of outer shells have been introduced in the fire service over the past years. Some have been chosen and trusted by active fire departments across the world, while others have failed to prove themselves.
Why?
Here's a quick look at what's inside your turnout gear, what fabrics work, what has failed in the past and some myths about outer shell performance and durability.
WHAT DOES THAT MEAN?
All PBI-blended outer shells offer
30 seconds
or more of break-open resistance, as shown in this Dynamic Flame Test.
By comparison, Nomex/Kevlar blends, such as Armor AP and Pioneer last only about 5 seconds.
Currently there are 4 PBI outer shells in North America:

IMPORTANCE OF TEAR STRENGTH
Turnout gear “wear and tear” is usually attributed to rips and tears and UV degradation. One of the best indicators of fabric durability is the NFPA 1971 Trapezoidal Tear Strength Test, which measures the pounds of force required to propagate a 1/3-inch tear in a fabric.
ALL fibers are impacted by UV, however PBI fabrics offer the highest tear strength properties, while PBO blends like Agility or carbon-blends like Tecgen 71 are weaker and show a rapid decrease in strength after exposure to UV.
Wearing fabric that test poorly can lead to a shorter life-span and increased cost of maintenance for the life of your turnout gear.
WHERE DOES FLAME PROTECTION COME FROM?
From THE FIBERS within
Flame resistance of any outer shell is determined by the decomposition temperature of the fibers within: the type of fiber and how much of it it's used.
The outer shells that offer the highest flame and break-open protection are those that contain ~40% PBI and ~60% Kevlar, because the decomposition temperature of PBI fiber far exceeds other fibers that make up fabrics such as Armor AP, Pioneer, Agility, Tecgen71.




How about
HEAT CONDUCTIVITY?
Another factor to consider when choosing an outer shell is thermal conductivity. Highly conductive fibers, like carbon and PBO, will increase the rate at which heat is transferred into the gear.
There are many reasons why PBO and carbon-based fabrics haven’t seen traction in the fire service since first being introduced in the 1990s. High thermal conductivity is one of them.
Outer shell fabrics like Agility and TECGEN 71 conduct high levels of heat very rapidly into the garment.
This thermal image depicts PBI Max and TECGEN71, simultaneously exposed to approximately 0.5 cal/cm2-s of radiant heat for 15 seconds.